cycle tester
as an engineering intern at OXO i was asked to create an easy to use life cycle testing system for housewares products. it had to be a compact unit allowing engineers to quickly set up tests for a wide range of products. the ease of use must extend to the physical setup of the machine’s gantry system, installation of pneumatic actuators, fixturing of the product, control the air system, and monitoring of the tests.
gantry
the cycle testing rig is built from aluminum extrusions and CNC water jet fixture plates. it features a gantry that can move within the entire volume on quick release sliders. all surfaces are designed to accept M5 bolts, either with t-nuts in the extrusions or in tapped holes on the custom fixture plates.

hardware
the hardware is integrated with the same m5 system. i designed custom water jet cut adapter plates for all pneumatic actuators, again interfacing with the M4 system. a rotary adapter was also made on the water jet to allow rotation of products or actuators off of the grid axes. i purchased a rolling cart to organize all hardware in the confined space.
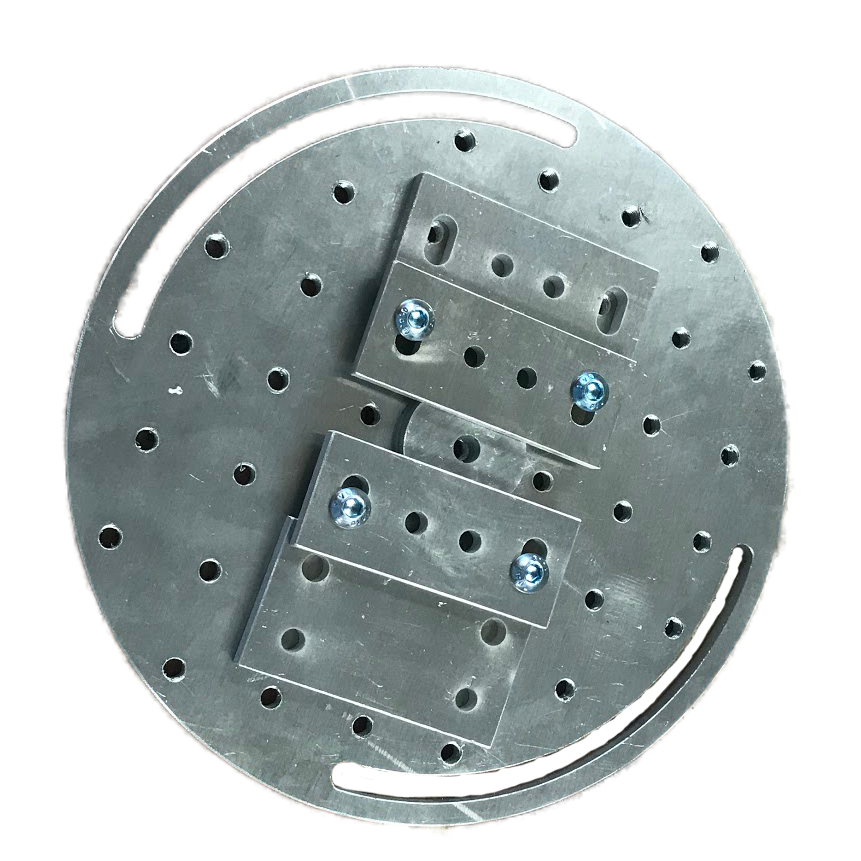
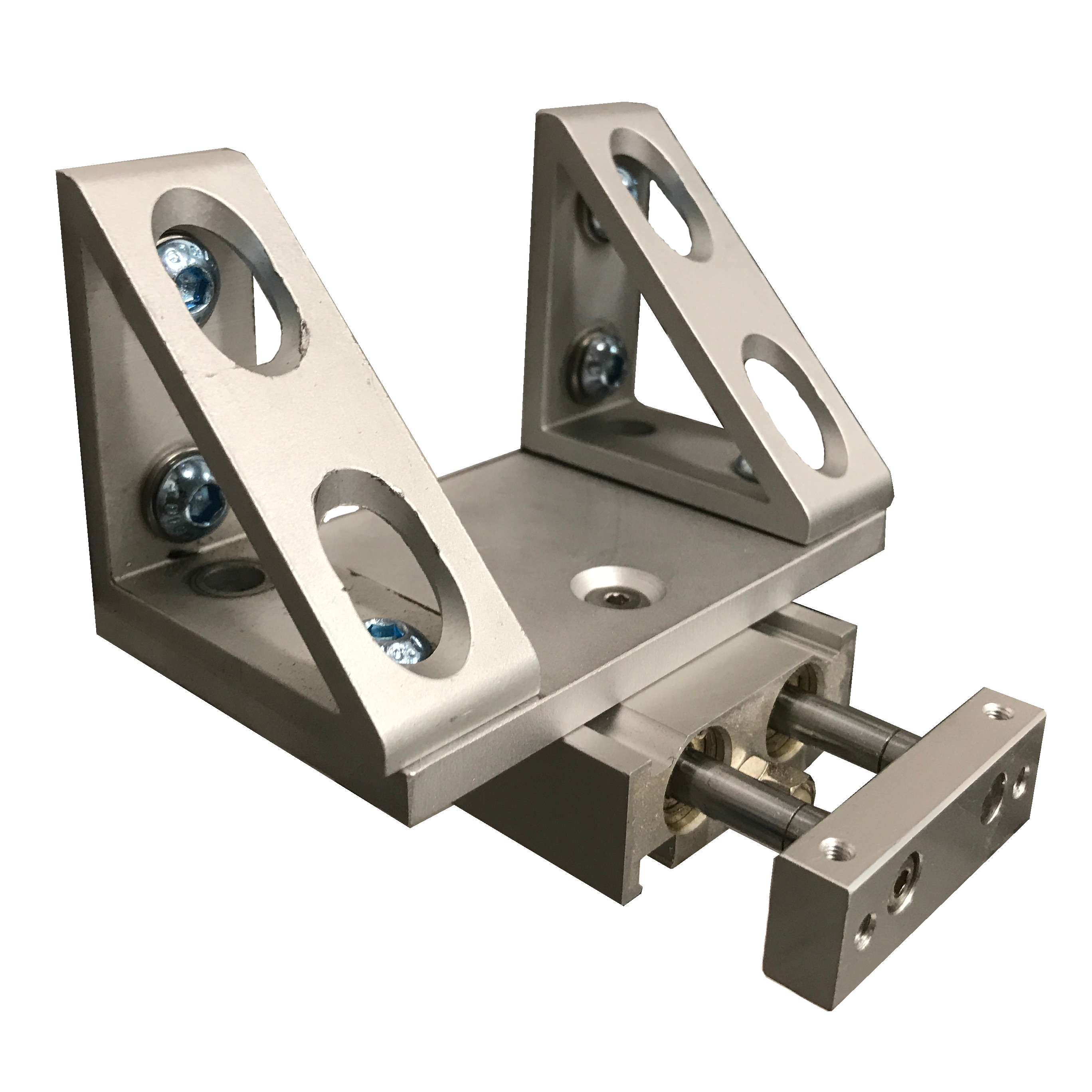
control
an arduino based control system triggers four independent air outputs via solenoid valves. each output is independently pressure regulated to allow tunable actuation force. a webcam is used for real time monitoring of test. the screen displays the number of cycles since the start of the test. momentary buttons allow manual on/off of each air line which is helpful in setting up new test configurations and pressures.
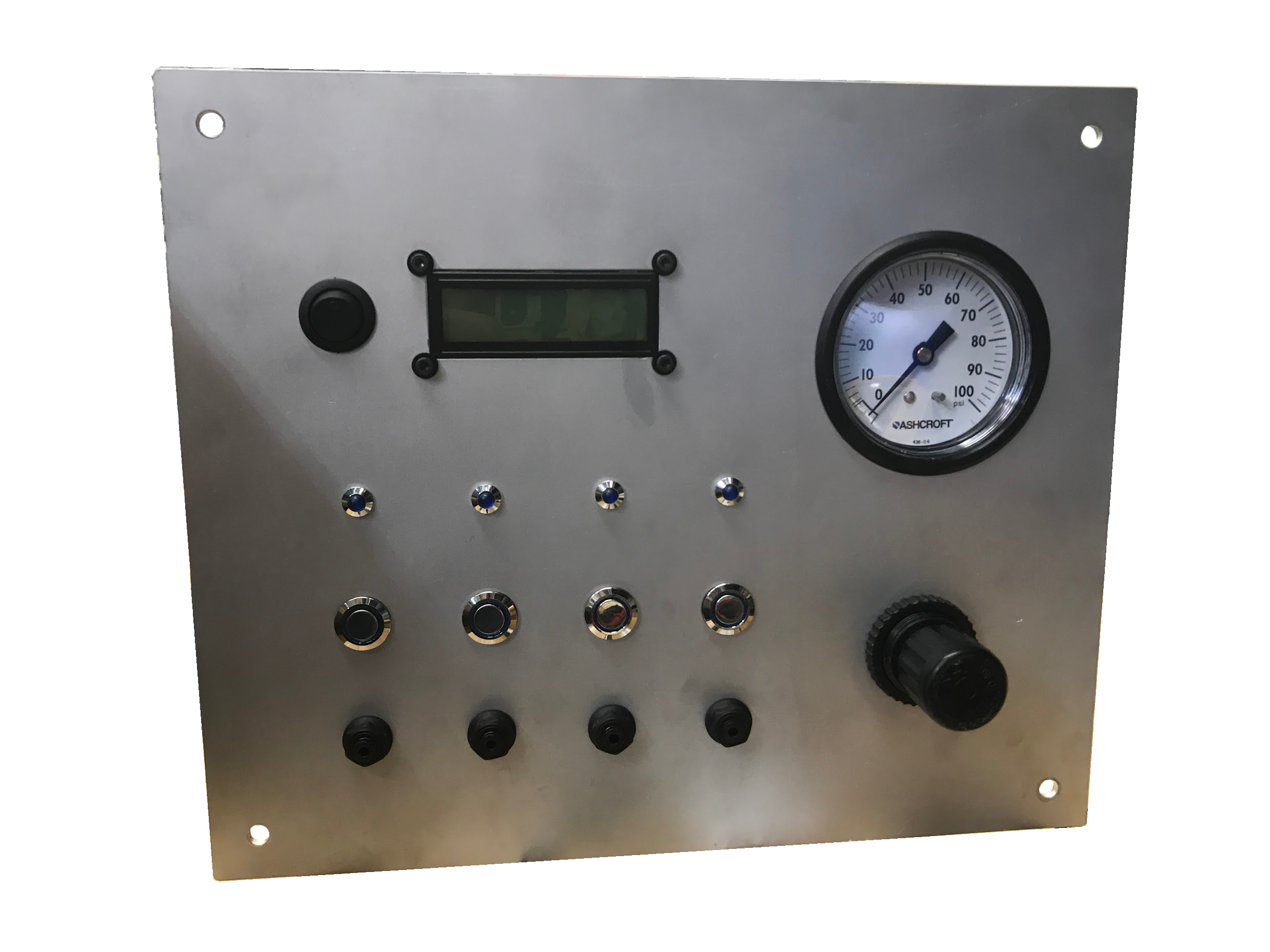
installed
i installed the cycle tester and hardware in the smaller engineering shop close to the product team bays. more in depth cycle testing is carried out in the quality control lab on another floor. for quick tests, this machine serves as a fast and easily configurable alternative close to the engineer’s work area.
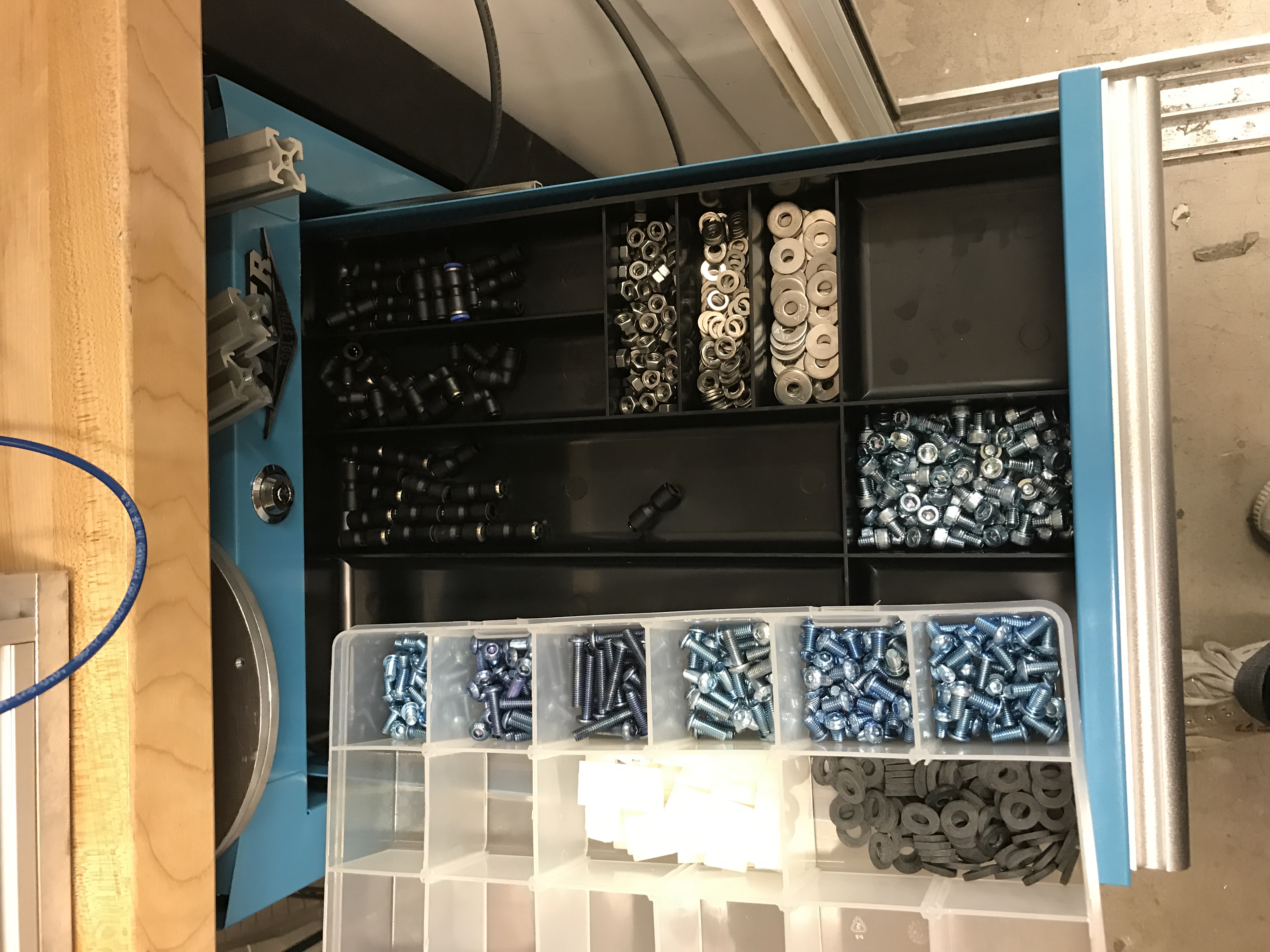
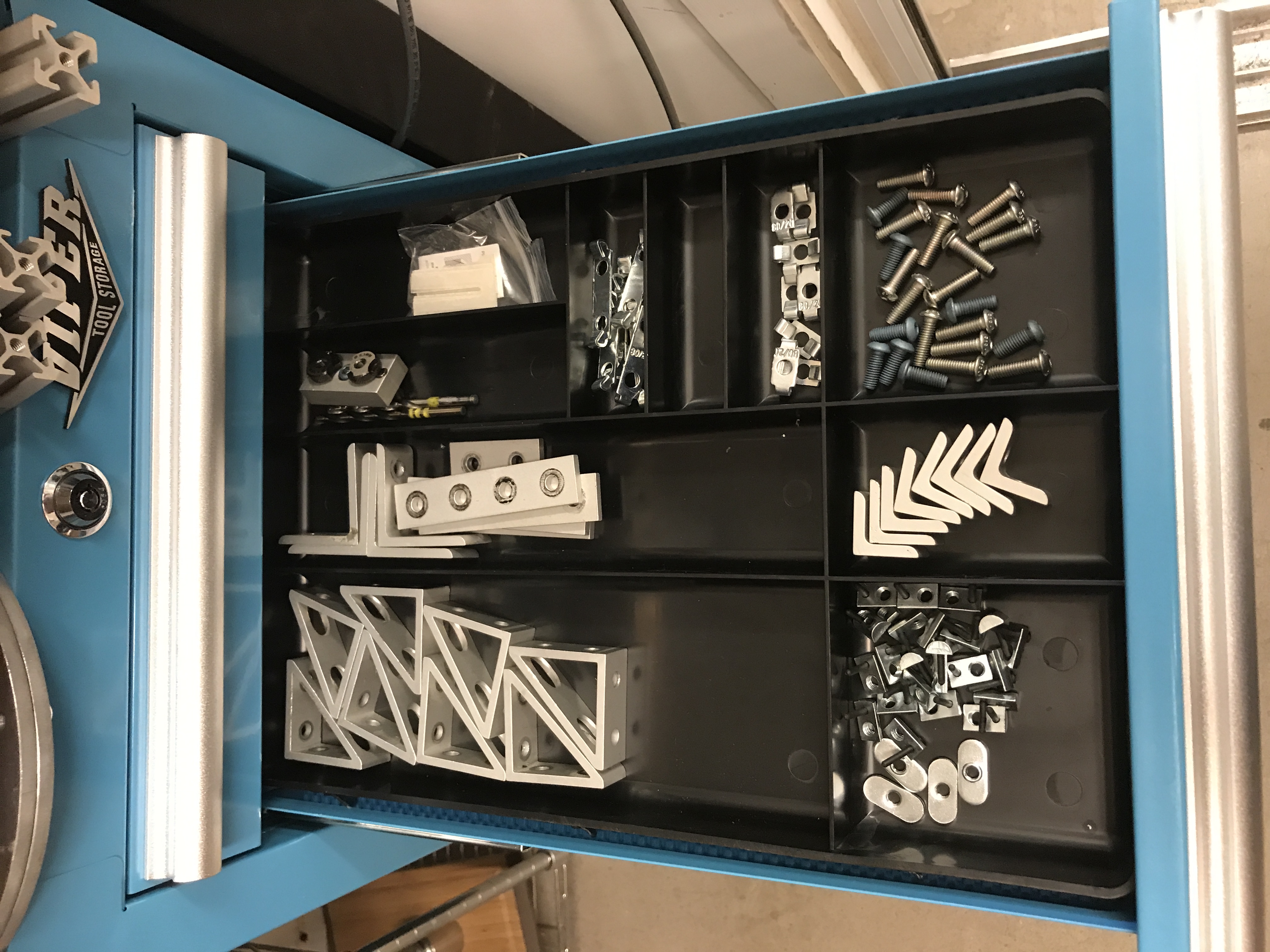
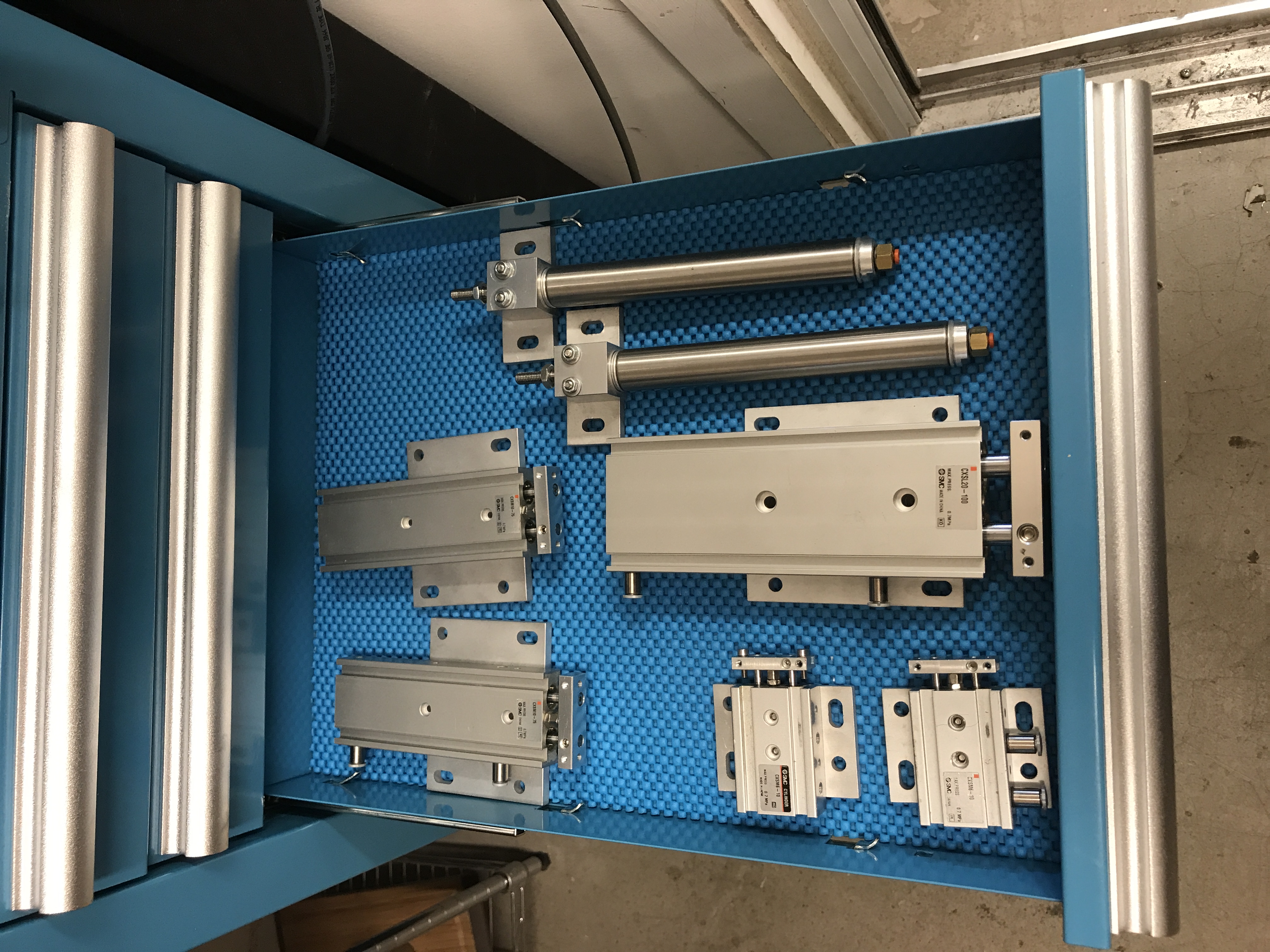
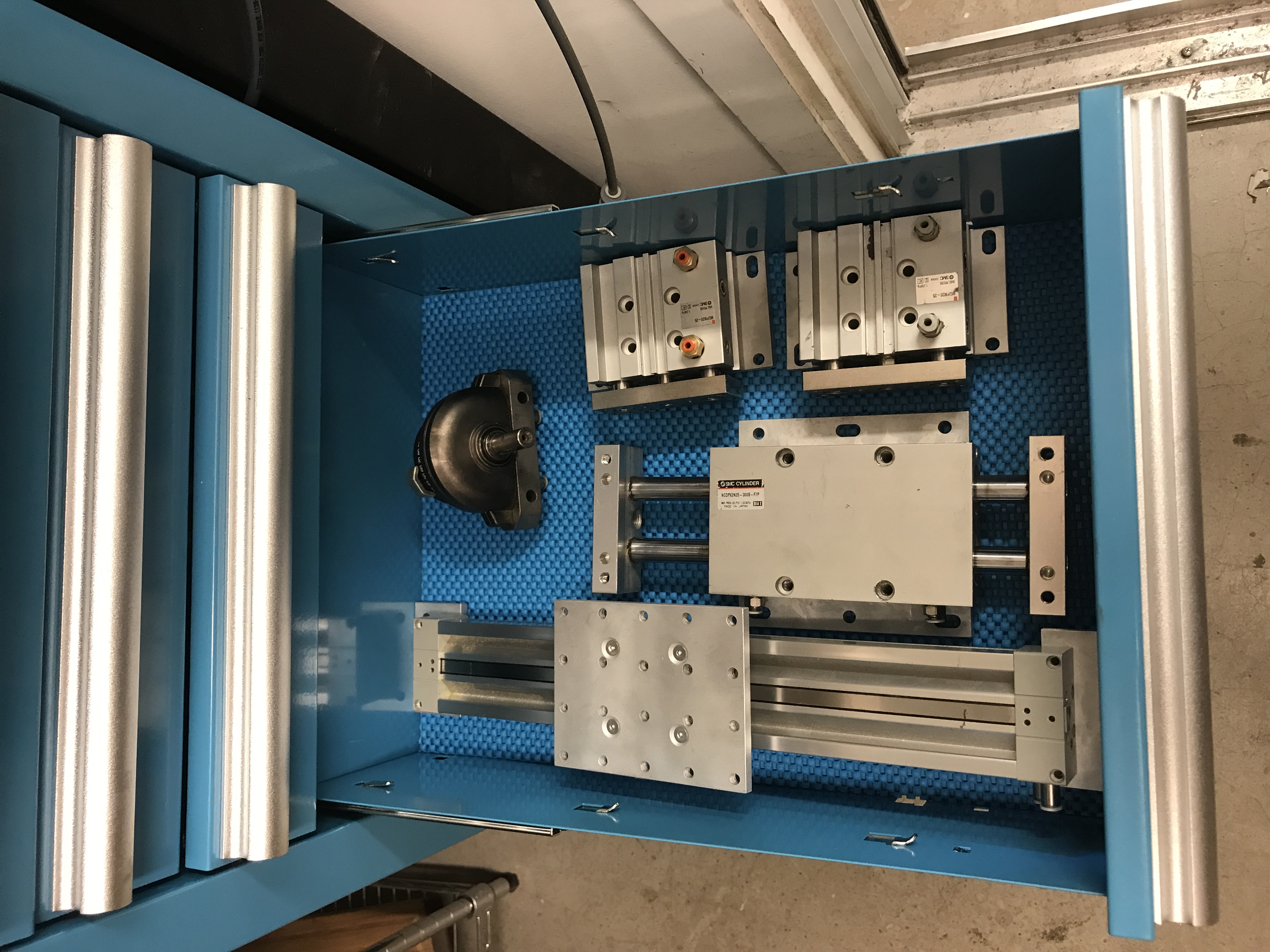